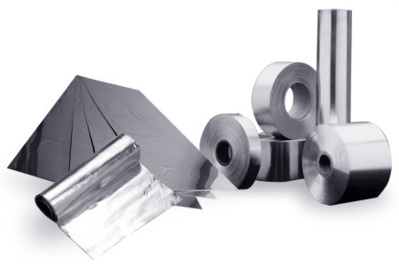
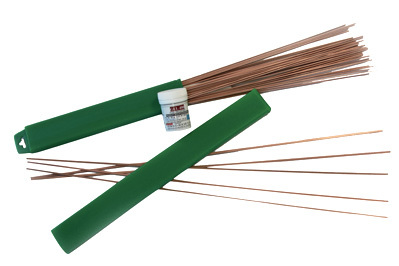
Silver, copper and phosphorus brazing alloys
The METACONCEPT Group offers two types of brazing alloys :
- High fluidity copper/phosphorous brazing alloys which can contain up to 15% of silver (preserving the mechanical properties at low temperatures)
- High resistance silver brazing alloys. Some silver brazing alloys are ATG approved.
These brazing alloys are often used with powder, paste and gel fluxes. Depending on the application, they are offered as bare or coated rods, bare or cored wires, laminates, tapes and preforms. These products are mainly used in construction and mechanical and electrical assemblies. For brazing alloys in cream form, please refer to the specific datasheet. Waste originating from the use of these products can be recycled. Contact our recycling department to find out more.
This table shows the most commonly used alloys.
Item no.
|
Designation
|
Composition
|
Dimensions
|
Solidis – Liquidus
|
Characteristics
|
Packaging
|
---|---|---|---|---|---|---|
RRRC1015
|
Rod LOMYPHOS
copper/phosphorous |
Cu93-P7
|
2 x 500 mm
|
710°C – 805°C
|
Good flowabilityé | 20 kg box |
RRRC1153
|
Rod LOMYPHOS
copper/phosphorous |
Cu93-P7
|
2 x 500 mm
|
710°C – 805°C
|
Good flowability | 1 kg box |
RRRC2158
|
Silver solder
2%, bare, cadmium-free |
Cu91- P7-Ag2
|
2 x 500 mm
|
650°C – 800°C
|
Good flowability | 1 kg box |
RRC52364*
|
Silver solder
6% ATG, bare, cadmium-free |
Cu87 – P7-Ag6
|
2 x 500 mm
|
650°C – 720°C
|
High fluidity | 500 g box |
RRRC2160
|
Silver solder
15%, bare, cadmium-free |
Cu80 – P5 –
Ag15 |
2 x 500 mm
|
650°C – 800°C
|
Good fluidity, good flowability | 1 kg box |
RRRA3050
|
Silver solder
30%, bare, cadmium-free |
Ag30 – Cu36 –
Zn32 – Sn2 |
2 x 500 mm
|
665°C – 755°C
|
Good fluidity, good flowability | 1 kg box |
AI000002**
|
Silver solder
34% ATG, bare, cadmium-free |
Ag34-Cu36-Zn27-Sn3
|
2 x 500 mm
|
630°C – 730°C
|
High fluidity | 500 g box |
RR100018***
|
Silver solder
40% ATG, bare, cadmium-free |
Ag40 – Cu30-
Zn28 – Sn2 |
2 x 500 mm
|
650°C – 710°C
|
High fluidity, very good flowability | 500 g box |
RR100019
|
Flux ATG AGFLUX
|
NC
|
NC
|
Zone d’utilisation 500°C- 800°C
|
Use with 6% ATG and 40% ATG solders | 80 g pot |
AI000003
|
Flux ATG CARBOFLUX
|
NC
|
NC
|
Zone d’utilisation 500°C – 800°C
|
Use with 34% ATG solders | 80 g pot |
RRA4400E
|
Silver solder
40%, coated, cadmium-free |
Ag40-Cu30-
Zn28-Sn2 |
2 x 500 mm
|
650°C – 710°C
|
High fluidity, very good flowability | 1 kg box |
RR100005
|
Silver solder
56%, coated, cadmium-free |
Ag56-Cu22-
Zn22-Sn2 |
3 x 500 mm
|
620°C – 655°C
|
High fluidity, very good flowability | 1 kg box |
RR100029
|
Silver solder
45%, coated, cadmium-free |
Ag45-Cu27-
Zn25-Sn3 |
2 x 500 mm
|
640°C – 680°C
|
High fluidity, very good flowability | 250 g box |
(*) ATG approved with AGFLUX flux (approval no.1530) for the capillary brazing of copper pipes designed for use in combustible gas installations.
(*) ATG approved with AGFLUX flux (approval no.1585) for the capillary brazing of copper pipes designed for combustible gas installations.
(*) ATG approved with AGFLUX flux (approval no.1530) for the capillary brazing of copper pipes designed for use in combustible gas installations.
Dimensions and weights are given for informational purposes only and may vary depending on the production run.
Have you defined the type of application? Contact us our staff will be happy to assist you in deciding which alloy to choose.
Designation
|
Metals being assembled
|
Comments
|
Forms
|
Applications
|
---|---|---|---|---|
Solder LOMYPHOS Cu/P
|
Pure copper or plumbing copper, copper alloys (brass)
|
Phosphorous acts as a flux on the copper. No need for an external flux. For copper alloys, you need to use an external flux.
|
Bare rods, ring wires preforms
|
Binary alloys mainly used in plumbing
|
Copper/phosphorous/silver solders
|
Copper and alloys
|
Requires an external flux. This brazing alloy is runnier thanks to the presence of silver which also preserves the mechanical characteristics at low temperatures.
|
Bare rods, ring wires preforms
|
Ternary alloys used in the manufacture and repair of electric motors and gas water heaters in the refrigeration sector. For this application, it is advisable to use a solder with a 50% silver content.
|
Silver solder for brazing
|
Steel, brass, bronze, nickel and copper alloys. All ferrous and non-ferrous metals, except for aluminium and magnesium.
|
Requires an external flux. Thanks to its high silver content which preserves the mechanical characteristics, this type of brazing alloy is runnier and has a lower melting temperature.
|
Bare or coated rods, bare wires in coils or on spools, rings, preforms
|
Alloys developed to replace alloys containing cadmium. Used in particular in the food or health sectors but also in mechanical and electrical assemblies.
|
Flux-cored silver solder for brazing.
|
Steel, brass, bronze, nickel and copper alloys. All ferrous and non-ferrous metals, except for aluminium and magnesium.
|
Tubular wire with 1% of integrated flux, perfectly controlled and constant. Non-corrosive flux, no cleaning required. Improvement to work quality. Significantly improved watertightness test.
|
Wires, spools, preforms and rings
|
Automotive industry, aeronautics, electrical and domestic equipment, copper or steel pipes, eyewear, jewellery.
|
The product safety datasheet below is available upon request from the METACONCEPT Group.
Before brazing, it is imperative that any layers of oxides are removed along with any impurities such as traces of rust, scale and verdigris. This procedure may be carried out mechanically (wire brush, sandpaper, grinder, file, etc.) or chemically.
Thick layers of grease or oil should be wiped off or removed using solvents (e.g. acetone) for sensitive parts.
To keep the parts being assembled in the correct position until the filler metal solidifies, they should be fixed ensuring that there is a narrow soldering gap between them of between 0.05 and 0.2 mm.
If the flux is contained within the coating or if the filler metal is auto-fluxing, you can proceed directly to the brazing stage described below. Otherwise, apply an external flux.
So that the filler metal can fill the gap, the parts being assembled must be heated to the working temperature of the filler metal (around 20 to 30° above the liquidus temperature).
As soon as the flux has been applied evenly and the temperature of the filler metal has been reached, apply the latter to the soldering gap.
The filler metal permeates the space between the two parts being assembled via capillary action.
The temperature of the filler metal must be reached within 3 minutes so as not to burn the flux, overheat the joint or damage the filler metal and the parts,
Leave the parts to cool in their holding brace until the alloy solidifies.
The part can then be removed from its support.
To avoid corrosion, flux residues must be removed after brazing using a wire brush or a piece of sandpaper.
The brazing alloy provides a highly durable assembly of parts made of copper, copper alloys or steel.
As the fusion temperatures are in excess of 600°, you must use a very powerful heat source such as an oxy acetylene torch for example.
To prevent burns caused by the molten metal, it is advisable to wear a protective apron, shoes, gloves, helmet and glasses.
- Do not smoke at the workstation.
- The workstation must be well ventilated.
- Wash your hands when leaving the workstation.
Comments :
Always use a flux suited to the intended use. Contact our technical department to ascertain which product is most suited to your application.All of the information contained in this document is provided for informational purposes only and the METACONCEPT Group will not be held liable for it.