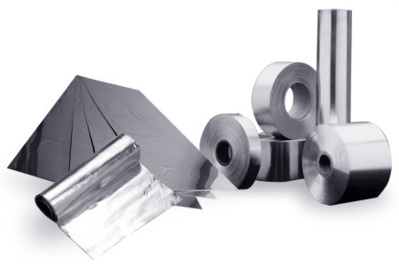
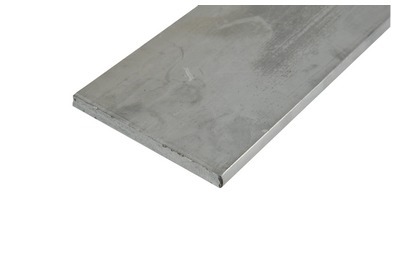
Zamak
Zamak is an alloy comprising zinc, aluminium, magnesium and sometimes copper. Its name is formed from the initials of these four components. Its melting point is around 400°C.
It is a resistant alloy that is easy to work with. Thanks to its stainless characteristic, it is ideal for die-casting as it has a very good fluidity and makes it possible to produce parts in very large quantities.
It is used in the automotive industry, for small mechanical constructions, toys, furniture, leather goods, costume jewellery and fashion (buckles for shoes and belts).
For small and medium-sized production runs, the METACONCEPT Group has developed a specific alloy for use in centrifugal processes with a centrifugal casting line. Its low cost and ease of implementation dramatically reduce manufacturing costs. You can find its main characteristics below.
Item no.
|
Designation
Dimensions |
Composition
|
Solidus /
Liquidus |
Recommended temperature in the crucible
|
Weight
|
Packaging
|
Comments
|
---|---|---|---|---|---|---|---|
CX100000
|
Zamak bar
400 x 100 x 10 mm |
Zn92 – Al4 –
Cu3 – Mg 0,5 |
380°C- 405°C
|
425°C
|
3 kg
|
Unit
|
Primary metals, excellent surface condition after casting
|
Dimensions and weights are given for informational purposes only and may vary depending on the production run.
It is advisable to use a type of silicone suited to the shape of the part being created. Have you defined the type of application ?
Contact us. Our technical staff will be happy to assist you in choosing which equipment and materials to use.
- Costume jewellery
- Figurines
- Modelling
- Miniatures
- Decoration, furniture
- Fashion accessories
- Leather goods
- Surface treatments (gold plating, silver plating, etc.)
- Mechanics, electricity: mainly for fixings
The product safety information sheet below is available upon request from the METACONCEPT Group.
Fusion in crucibles or tanks.
It is advisable to empty the crucible of one third of its total volume before refilling it with new alloys or with “cores”.
Fill it up to the correct level, allow the bath to return to its original temperature then mix the alloy well by creating a vortex.
To prevent burns caused by the molten metal, it is advisable to wear a protective apron, shoes, gloves, helmet and glasses.
- Do not smoke at the workstation.
- The workstation must be well ventilated.
- Wash your hands when leaving the workstation.
Comments :
Always use a flux suited to the intended use. Contact our technical department to ascertain which product is most suited to your application.All of the information contained in this document is provided for informational purposes only and the METACONCEPT Group will not be held liable for it.